The New 3D TSV FABCO by TrussCast Portable Batch Plant
Factory for Pre Finished Total Pre-Cast makes the UltraLavaFibers system now available world
wide. The pre finished and pre-wired and pre-plumbed super insulated Eps R 4 per inch or urathane R7 plus
per inch panels ( 6 inch wall is over R 30 ) with less than 3 % heat loss. Panels with steel connector lift systems
are built in 4 by 8ft. , to 10 by 40 ft. wall panels and 1 by 16 to 10 by 40 ft. floor and roof panels
that makes it the absolute fastest and most economical all concrete luxury building system ever. All buildings
will offer outstanding high style architecture with wide span rooms with high ceilings with designer lifetime finishes.
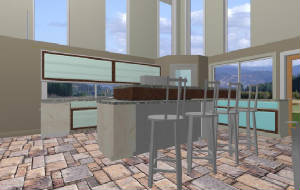
Our total
designing and building system is unique to our company. Many companies offer some pre-cast or tilt up systems but most still have to be finished by hand in the old traditional time
consuming ways. All the real time consuming operations such as insulating, electrical, plumbing, and air conditioning,
installing brick, tile, stone, dry wall, cabinets, counter top, electrical and plumbing and air conditioning trim
out, molding trim, doors, windows etc are all very time consuming especially in a multi level building. In the traditional
building systems none of these operations can be done until the structure is built. In our system they can be built
at the same time the preliminary site preperation and foundation is going in (saving many months). In traditional projects,
cost and construction time is still in the 10 to 24 month project scheduling, due much to weather delays ands the fact
that most operations have to be completed before the rest can be done. Also the loss from stolen and material damage from trying
to site warehouse and move all the materials up stair ways during the construction process adds to the cost.
The out of date old methods of on site construction scheduling is no longer affordable and the resulting buildings
are very inferior to ours, due to the fact that doing things up in the air on site is not nearly as fast as factory
conditions. The price of factory wages that in many cases are assisted by the government training programs, makes
total cost much less that traditional high priced sub contractors wages, hugh bonding costs, sub contractors builders
risk insurance, exsorbant high rise workman comp insurance and extra sales taxes and middlemen deliver
and marketing fees. In normal construction the shell erection and finishing can not happen until other events happen,
We are able to shave months off of the construction schedule (6 to 12 months quicker occupancy can mean million of dollars
in savings and huge fast revenue advantage ) by pre-building in the factory all the real time consuming operations
happen simultainous off site, while the clearing and pre landscaping, permitting, under building utlilities, parking
foundations and utilities are going in. We also save by buying bulk price materials as an Original Equipment Manufacturer
(OEM pricing) and manufacturing much of the products that would would normally have 2 or 3 stages of distributor, dealer and
sales commissions figure into the cost.
We can
build much better quality luxury granite kitchens and baths that, would cost $1000's more if built on site,
they also have 95 % of the wiring and electrical, breakers, plumbing, venting, and air conditioning ready to go
when set by crane in just a few weeks. Building in factory controlled conditions gives a much better fit
and finishes, at lower overall price. There are very few companies that even offer prefinished panels, none I know
of that do our total designed , pre-wired, pre-engineered and factory pre-built modular concrete core kitchens baths
and closets.
Modular
pre-finished , kitchen and bath-closet cores and foam core concrete sip panels can save millions of dollars in material and
time saved while building the best class of all reinforced concrete towers, commercial buildings and better
home construction. We also can build parking garages and commercial projects with regular unfinished
hollow core panels for spans up to 60
feet between spans.
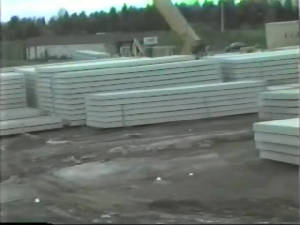
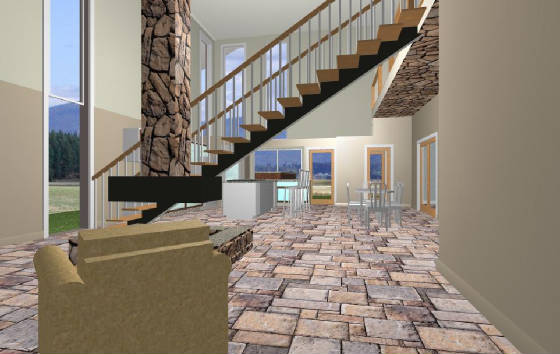
Top floor penthouses have soaring 20 high ceilings with skylights and dramatic real wood fireplaces and unique
designer stairs to huge loft media room and guest suite/office. All units have main living on one level with mansion size
rooms and a front lock out guest suite or office on main level with master bedroom and spacious mansion sized living
kitchen family room with full super insulated glass wall bring the beautiful outdoors in with large 10 feet by
20 feet designer concrete decks some with additional deck from lofts and master bedroom on first floor. Creative lighting
is offered as options in Glass block areas of Baths and aquarium walls and
under counter lighting in the huge serving bar.

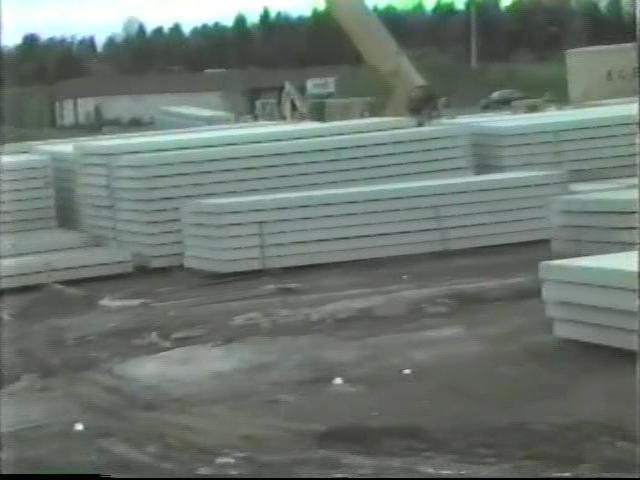
We can also bring our molds and casting methods to large sites for on site production where shipping distances are more
costly and there is large parking lot or tennis courts for on site panel casting. The finishing options are more limited
but still far superior to any other precast options.
100,000 plus sq. ft plant planned for Gulf Pre-cast in affiliation with Weiler ( http://www. weiler.net) The State of the Art Pre-Cast plant is to be located on the coastal water way and on Rail and major freeway
systems, for the most economical shipping to much of the USA and world markets.
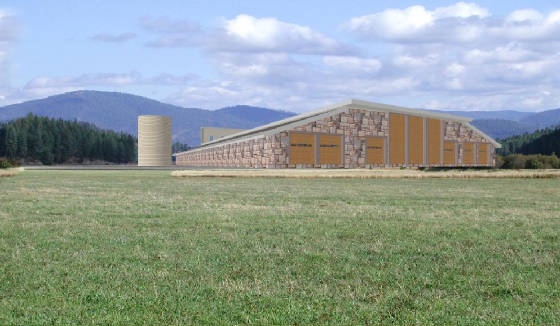
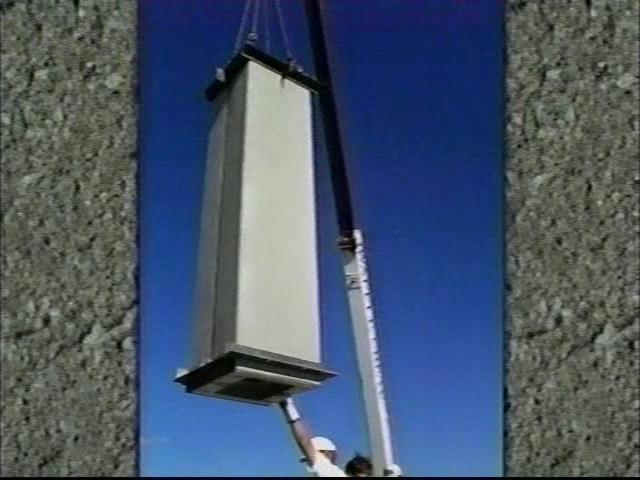
Precast thin wall hollow (designer finished on the outside) columns and beams allows erection to continue with out waiting
for complete cure of structural reinforced colums and perimeter structural bond beams that tie the whole structure together
and acts as one monolithic poured reinforced structure providing tremendous additional earthquake and storm protection similar
systems, not nearly as strong as our panels and beams tested to 5 richter and 220 + miles per hour winds.
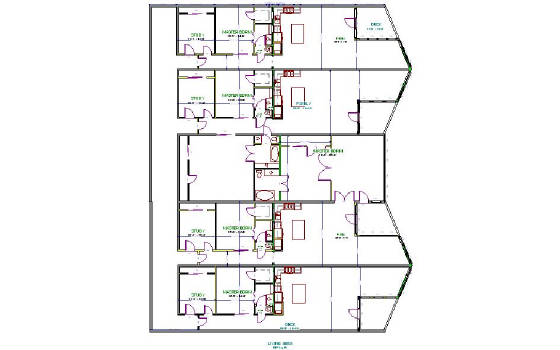
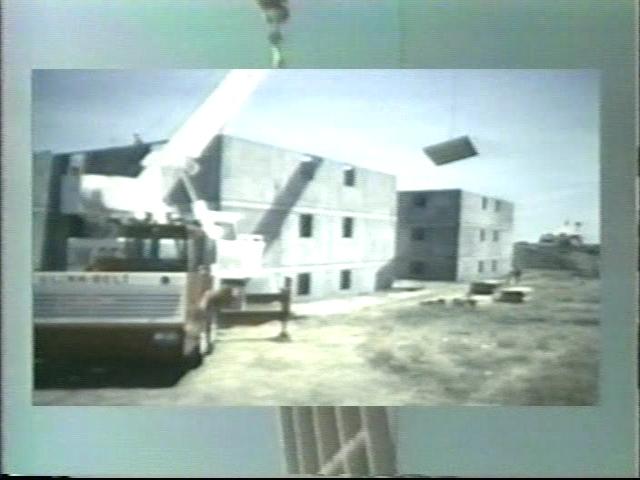
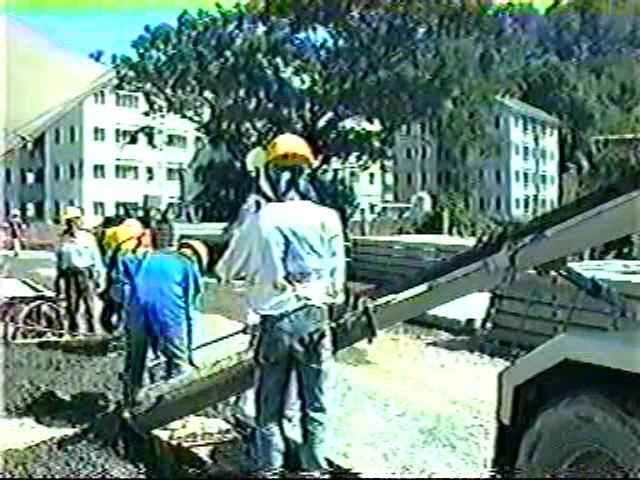
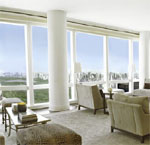
Tempered @ glass storm glass is bonded to stuctural precast
high strength graphite, carbon fiber-nylon concrete frames that are factory molded in one continuous wall with
designer step back trim for the best in beauty, open feel, and with r 4 insulation ( most windows less than r 1 and
great noise reduction with 1 1/2" in doors and 4" of separation of storm bonded structural storm glazing.
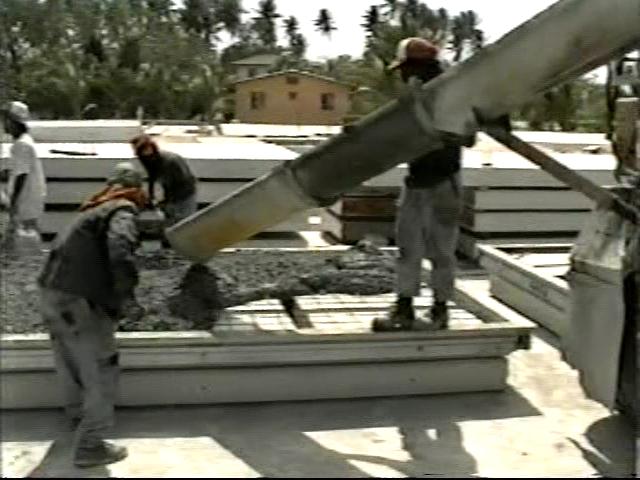
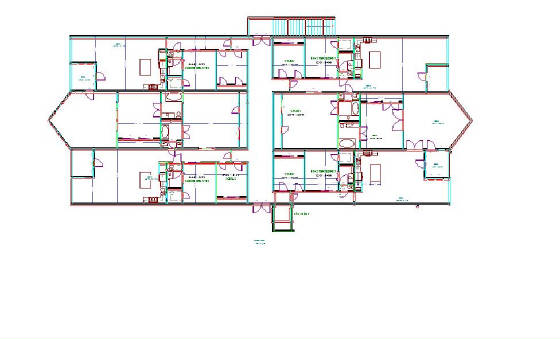
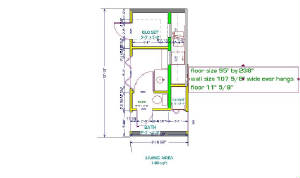
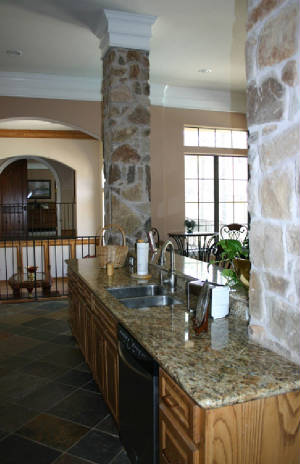
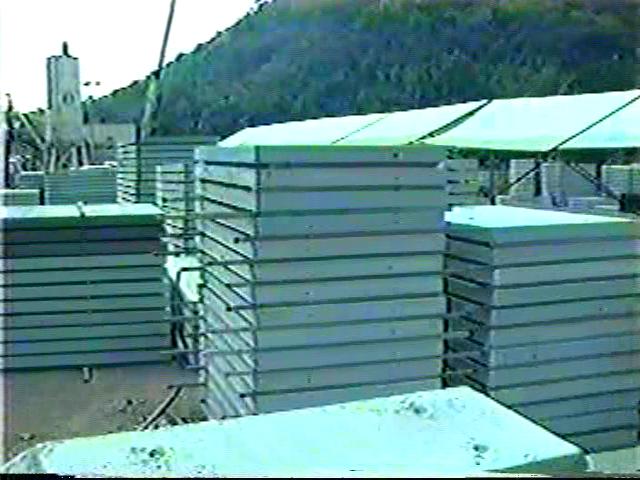
Hollow Core Pre-stressed Floor and Roof panels are built in 4 feet to 8 feet wide and
up to 60 feet long panels 4 to 16 inches thick. These are not pre-finished but are readily available now from the giant
Houston Precast Plant which casts to our specs and delivered factory direct to job site. Our new pre-finished
wall and glass panels are now available in smaller quantanty from our Conroe Pre-cast Column, Pier, Beam, Wall, Floor,
and Roof Sip Precast Plant. Offering 10 to 16 feet wide and up to 40 feet long in Pre Finished foam core ultracrete
Pre- finished Pre-wired Wall, Floor, and Roof Panels. The Super Glass deck side end walls have "E" tempered glass set
in structural glazing in graphite or carbon, or nylon fiber reinforced concrete and separated by one and one half inch
to four inches of dead air space between panes for the best noise and insulation factors. Our propietary system
gives us great cost to value as we are the OEM manufacturer of the ultra Energy Windows and Doors. The hallway and glass
deck side end walls have 1 1/2 inch spacing beween glass panes in the doors and the windows have up to 4
inches inches between glass in the window sections, the deck side end frame walls have 2 to 6 inches of
foam in the core sandwiched between 2 layers of structurally engineered steel reinforced Ultra Fume Crete made with
our super formula high density high strength Ultra Crete with additives and Graphite- Carbon , steel, and
nylon fiber reinforcing in the concrete on both interior and exterior surfaces. The windows have unique step back
designer trim cast into the panels and require no futher finish. Surfaces may be smooth finished stucco or any type of texture
or the walls and floors may have exposed rock or sandblasted granite like aggregate finish. The panels can
be pre-finished, pre-wired, and pre-plumbed. We also can economically put a realistic stone or tile pattern and stains
on the concrete with our unique roller system adding greatly increase style look and cost advantages. See http://www.quickimprint.com for finishing choices for the wall, floor, and roof (panels may use EPS closed cell foam or urathane or light weight agregate
and air entraned concrete cores for the panels. The prefinish Designer Shell Columns and Shell Beams are site filled in the
high rise structures to give a complete monolithic concrete structure with the maximum sheer ratings. We also build complete
all Concrete steel reinforced Piers and Beams or Post Tension Beams depending on engineering requirements. They are used
in our deep pier foundation system. All Wall and Floor panels have Continous Structural Concrete around the perimeter
of sip panels with the super high strength Ultra Crete Concrete that has a minimum over 5000 psi low slump
high strengh high density concrete with is impervious to salt water and steel corrosion with up 6 to 8000 psi
for beach front locations and up to 18,000 psi for super high rise construction. The Concrete Beam
designs in panels goes completely around the perimeter and has concrete/steel reinforced studs as needed
with special steel reinforcing between the foam core panels which bonds completely to the Ultra Crete Fume high density
concrete to create a continuous truss wall of unbelievable strength. The ultra crete fume crete is also used in the unique
hollow shell Columns and Beams which are site filled with high strength concrete to create a complete monolitic maximum sheer
strength building that needs no futher finishing. They are site filled with high strength Ultra Fume Crete. This
allows us to build high strength structural panels up to 16 feet wide by 60 feet long,roof panels can
be prefinished with Designer Tile Roofs with 4 inches to 10 inches of foam cores with radiant barrier for the ultimate
in energy efficiency offering up to R 60 values in 16 inches thick Panels that can span up to 60 feet with over 100
lb live loads and meet and exceed 5 R. and over earth quake rating and with stand the strong hurricanes and tornados.
They also give the best insurance and fire ratings and are insect and mold free. Most of our coastal beach front
properties will have 2 levels of parking on first floors to allow storm surge to flow thur the building and not push
against the building cast into the deep pier foundations that become monolithic concrete according to Extensive
sheer and earthquake testing. All of our buildings have reinforced structural concrete beams built into
the Sip panels on top, bottom and sides of the panel and concrete studs 2' to 8' feet on center depending on loading
and span. The out side and inside of the pre-finished panels will have 1 to 3 inches of reinforced special low
slump, some nearly 0 or 1 or 2 slump mix that will be vibrated and compacted in unique metal slip forms sytems patents. The
proprietary formulas and special curing techniques yields high strengh concrete nearly twice the PSI strength of normal
porous site pumped and poured concrete. We can design mixes with a PSI of over 18,000 (normal concrete is
2000 to 3000 PSI> Concrete block often only 1000 PSI. Some panel designs will have super graphite,
carbon, steel or nylon fibers and special additives such as fly ash, silica fume and other air entrainied and poly additives. All
will be pre- engineered and stamped, so they will be acceptable in any building code. Monitored By the Internationally
approved PCI Testing institute. The panels and pre-enginered beams will be prefinished on both sides in many unique
architectural effects ranging from smooth, sand stucco, stone , brick, tile patterned etc. The panels can be pre- wired
and pre-plumbed. The welded and high strength bolted heavy duty connections (Stainless optioned on Coastal areas) Connectors
and pick up points are often welded to the rebar or tensioned cables. This is the key to our high rise capablities.
The small contractors and home builders can use our small modular 4 by 8 foot and 4 by 10 foot light weight panels that
can be set with light fork lift equipment, while the larger 8 to 12 feet wide by 20 feet to 40 feet long
with some designed for up to 60 feet spans. The SIP panels will be set by crane by PCI certified errectors. Most panels
and beams over 20- foot long will be post tensioned or pre tensioned panels.
We also use hollow core panels on the larger spans on parking garages and large office commercial jobs. We are planning
on also building large hollow core casting lines at our modular plants in Texas, Louisianna, Mississippi, and the Gulf Coast
factories. We will joint venture or licence plants in most major cities. We are building and additional
very large plant In Conroe Texas (Woodlands/Houston Area) t to build our modular concrete kitchen and bath cores and Sips,
and 8' feet wide hollow core panels . We will be building our luxury concrete walled and floored granite kitchen
and bath cores on 8 to 10 feet wide by 20 to 40 feet long reinforced concrete modules. Factory precision and quality
control also saves many month of construction delays. Erectors can erect the towers many month faster than
building conventional with wood, steel or concrete block or any poured in place system.
Good crane operators can erect a floor a week with this system. We can be doing most of the work indoors
with out weather delays, while getting the legal work, soil testing, envionmental studies and market analyis and
site development done. The building can be errected 95% complete in record time. We also have plans and partners
to build a 100,000 +sq. ft plant in Mississippi on the river on the inter coastal ship channel to
allow low cost barge shipping to over 25% of us cities and many foreign countries.
All exterior roof and floor panels will be pre-cast pre-insulated with polystrene EPS or urathane foam core
radiant resistant panels. They will be built in sizes ranging from 4' to 16' wide
most cost advantage is 10 feet wide panels and can be up to 16' wide by 60' feet long and will be set by
more affordable modest size crane. Each plant will have their own cranes for low cost erection. The new complete automated
$10 million dollar plants will build the Pre cast Concrete Modular factory to build Luxury Kitchens and Baths modular cores
which are completely wired and have appliances and unique Split Rotary super long live efficient heat/rotary Air Conditioning
System which has all ducting in the insulated area instead of the attics as most systems use. This alone can save
10 to 30 % on heating and Air Conditioning Cost. We will offer optional
loop geo-therm cooling on high end projects where practical.
Building will be designed to take of advantage of natural Solar advantages. The Plants will manufacture
complete designer architectural Sip panels as well as the high volume hollow core pre-stressed with pre- finish on one
side only ( will also have foam options. ) This is the first all concrete modular plant designed to build luxury
tower buildings of mid to high rise. At least we don't know of any yet. This is the key to building affordable luxury
Towers and save on Parking lots preparations and high site costs. This is only possible with large scale projects designed
by our affiliated architects and engineers licensed by UltraCrete Precast Co. This system allows creative archtects and
engineers to build nearly and y style of high fashion designs with fantastic news worth projects in record time.
This gives us many more options on finding affordable great view and great location sites for the Unique Retirement Luxury
Tower Concept and
build Exciting Hotels, Condos, offices, Churches, and any commercial buildngs in record time as the building are
built in high precision factory conditions with lower cost trained skilled and low cost helper factory workers
and the advantage of manufacturing nearly all major cost items in record time and cutting out all major high priced sub contractors
and saving many layers of cost in materials and fixtures by buying and selling factory direct, cutting out many
middle mens profits, as well as double and triple freight factors. By the time the legal and site utility
development is completed the building can be errected to nearly 95 % completion in weeks instead of months or years.
This saves millions on Luxury Towers, in sub contract , material, and interest and greatly increasing
the profitablity by the quick occupancy.
Sips plants are being built in Texas, and Mississippi . The plants will use some equipment by Echo Engineering
and all our pre-casting plants will be PCI certified.
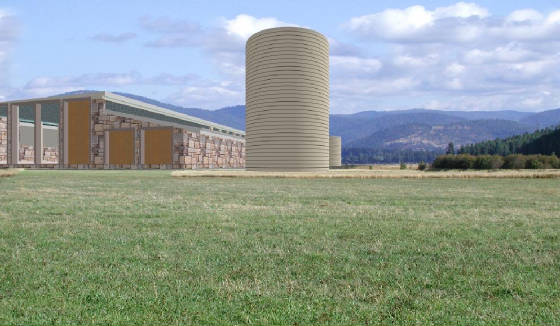
factory will have 4 lines of pre cast pre finished
Luxury Bath and Kitchen Cores that are ready to live in. They are completely wired and plumbed.
Picture of high tech equipment for 600 foot long 10 bed casting lines.
|