Scroll down
to bottom of page
and return to side menu
Optional site casting systems that use TSVFABCO Molds and portable TSV batch plants with license from UltraLavaCrete
Co. for remote located projects is now available for one to ten story construction. Orders pending for
Belize, Serra Leone, Ghana etc.
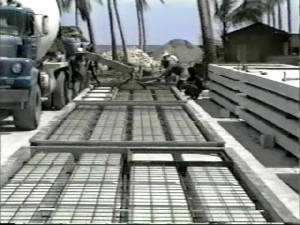
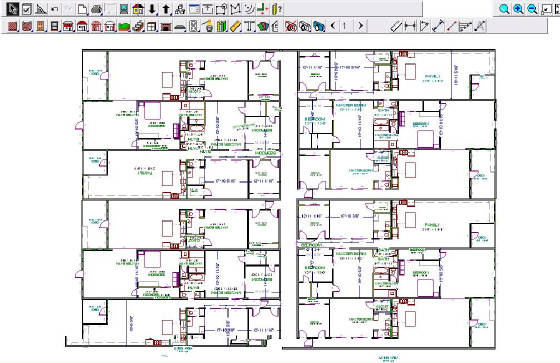
One side of Twin Towers for 8 units per floor
per tower
Floor plan for 1500 to 2300 sg ft condos
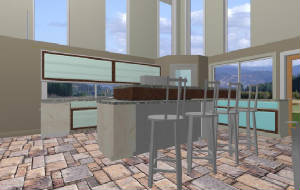
Our total
designing and building system is unique to our company. Many companies offer some pre-cast or tilt up systems but most still have to be finished by hand in the old traditional time
consuming ways. All the real time consuming operations such as insulating, electrical, plumbing, and air conditioning,
installing brick, tile, stone, dry wall, cabinets, counter top, electrical and plumbing and air conditioning,
duct sytems, base and trim out, molding trim, doors, windows etc are all very time consuming especially in a multi level
building. In the traditional building systems none of these operations can be done until the structure is built.
In our system they can be built 24 hours a day 7 days a week on the ground in precise factory controlled conditions and erected
in just days instead of months, and at the same
time the preliminary site preparation and foundation is going in (saving many months). In traditional large multi level
projects, cost and construction time is still in the 10 to 24 month project scheduling, due much to weather delays
and the fact that most operations have to be completed before the rest can be done. Single family homes can be erected injust
a few days after site prep.
Also the loss from stolen and material damage from trying to site warehouse and move all the materials up
stair ways or costly crane time during the construction process adds greatly to the cost. The out of date
old methods of on site construction scheduling is no longer affordable and the resulting buildings are very inferior
to ours. Due to the fact that doing things up in the air on site is much more complicated and much more expensive and
not nearly as fast as factory conditions. The price of factory wages in many cases are assisted by the government
training programs, makes total cost much less that traditional high priced sub contractors wages, hugh bonding costs,
sub contractors builders risk insurance, exsorbant high rise workman comp insurance and extra sales taxes and
middlemen multi location warehouse deliver and marketing fees. In normal construction the shell erection
and finishing can not happen until many other events happen. We are able to shave months off of the construction schedule
of large multi building projects (6 to 12 months quicker occupancy can mean million of dollars in savings and huge revenue
cash flow advantages ) by pre-building in the factory 24-7 all the real time consuming operations happen at the
same time as the off site preparations are being done. Many times the pre-built pre- finished kitchen and bath
modules with all the airconditioning, wiring, switches, and the exotic designer finished concrete panels can be built before
a normal project could even schedule the first stage of construction. With our system the building can be ready to set
by a crane in just weeks, with 95% of the building
already built, All this can be completed while the clearing and land preparations, soil compaction permitting, under building utlilities, parking foundations
and utilities are going in a normal project. We also save by buying bulk price materials as an Original Equipment Manufacturer
(OEM pricing) saving many stages of manufacture to distributor to dealer to builder to owner distribution cost and delivery
expense. In our system we are manufacturing much of the products that would would normally have 2 or 3 stages of
distributor, dealer and sales commissions and multiple freight costs figure into the cost.
We can
build much better quality luxury granite kitchens and baths that, would cost $10,000's more if built on site, in
our system we also have 95 % of the wiring and electrical, breakers, plumbing, venting, hotwater heating,
all appliances and air conditioning installed and ready to set by crane in just one lift and in just a few weeks erection
schedule. Building in factory controlled conditions gives a much better fit and finishes, dramatic architecture
with high ceilings Dramatic windows and sky lights with life time exotic stone like finishes that would be many
times higher cost in normal construction. There are very few companies that even offer prefinished panels, none
I know of that do our total designed , pre-wired, pre-engineered and factory pre-built modular concrete core kitchens
baths and closets.
Modular
pre-finished , kitchen and bath-closet cores and foam core concrete sip panels can save millions of dollars in material and
time saved while building the best class of all reinforced concrete towers, commercial buildings and better
home construction. We also can build parking garages and commercial projects with regular unfinished
hollow core panels for spans up to 60
feet between spans.
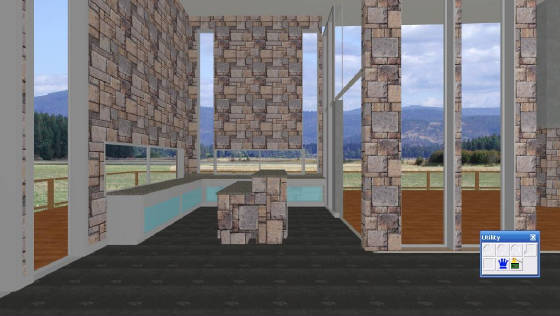
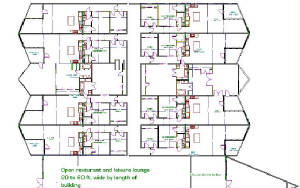
|